The rise of 3D printing means it’s now easy to create objects to any design we like from scratch, something that’s already finding particular use in medicine, with 3D printed customised prosthetics or even replacement bones such as hip joints. Going one step further is to create so-called “4D printed materials” that once created can change their shape.
Following decades of research by chemists, engineers, physicists and biologists this promising field of “smart materials” includes polymer-based (plastic) materials that can drastically change their properties if triggered by changing environmental factors such as heat, moisture or pH. Now, in a recently published paper, US researchers have demonstrated novel smart materials that can be pre-programmed to shape-shift in specific ways, without the need for an external stimulus to trigger the change.
Smart polymers have been put to many uses. For example, as nanoparticles that only form when a solution is shaken, or dissolve to release a pharmaceutical when the nanoparticle is taken up by a living cell. Or nanoparticles that shape-shift into a different type of nanoparticle when the temperature changes, and shape-shift back again when the temperature change is reversed. On a much larger scale, smart materials have been used to create self-healing systems, where the mechanical forces that cause breakages also initialise chemical reactions that glue two broken pieces back together.
What all these smart materials have in common is that they only react to external stimulation. Being able to “program” smart materials to shape-shift without a trigger, as demonstrated in the new paper, is a new achievement.
Pitting physical against chemical
Published in Nature Communications, the study focuses on the preparation of cylinder-shaped polymer hydrogels: soft pieces of plastic that contain water, similar to the material soft contact lenses are made from.
The usual mechanical behaviour of these plastic cylinders relies on its chemical structure, made up of two sets of bonds between individual chains of polymers. The first type of bonds that hold the cylinder material together are known as chemical crosslinks, which are permanent and do normally not break. The second are the many physical hydrogen bonds that hold the plastic cylinder together. Crucially, while initially stable, these hydrogen bonds can be broken under sufficient stress, becoming soft and then reforming in a different configuration.
Xiaobo Hu et al/Nature
Left for enough time – perhaps days – this material will eventually assume the shape in which the strong chemical crosslinks are least strained. This is just the same as how a rubber band returns to its original resting shape after having been stretched (only a rubber band moves much faster).
In the study, the researchers forced one of their smart material cylinders into a specific shape for a period of time. While deformed, the material’s chemical structure attempts to reform into its original shape, just as a rubber band does. However, depending on how long the cylinder is bent out of shape, the physical hydrogen bonds inside the material will break and reform in a way that actually favours the new, bent, shape.
When released, an internal struggle begins inside the cylinder during which its chemical structure attempts to revert to its original shape, but to do so requires the physical network of hydrogen bonds to revert to its original form, which can take some time.
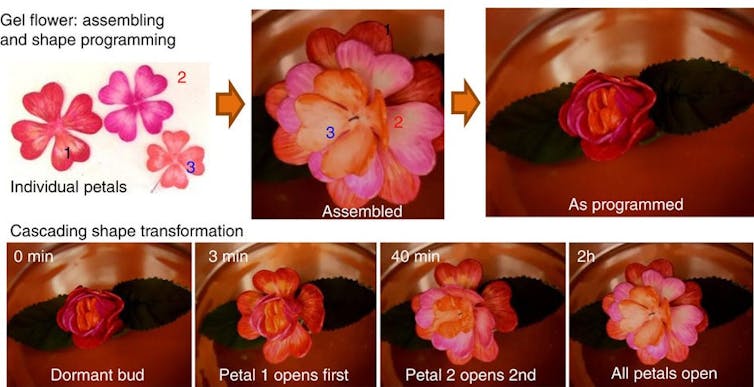
Xiaobo Hu et al/Nature
Timing is crucial
The authors demonstrated that the time the material requires to revert to its original shape depends on how long it is held bent out of shape. The longer it spends deformed, the more the physical connections become accustomed to the new change and the longer it takes for the cylinder to relax back.
Impressively, this means the researchers were able to show that one of their smart material cylinders could be programmed to perform a specific routine by applying several bends, each held for different lengths of time. They were also able to program a time lag, applying a thin water-soluble coating to the cylinder which prevents the cylinder from starting its shape-shifting until the coating becomes soft from immersion in water.
Given the large and growing interest in smart materials, this research offers an interesting new approach to their design and manipulation. Adding the element of timing and trigger-free activation into the design of smart materials offers all sorts of uses, for example home products that adapt to heat or moisture. And of course there’s enormous potential for biomedical treatments, such as minimally invasive surgical procedures, autonomous actuators, slow-release methods for drugs, or physical implants that respond to environmental changes, even within the body.